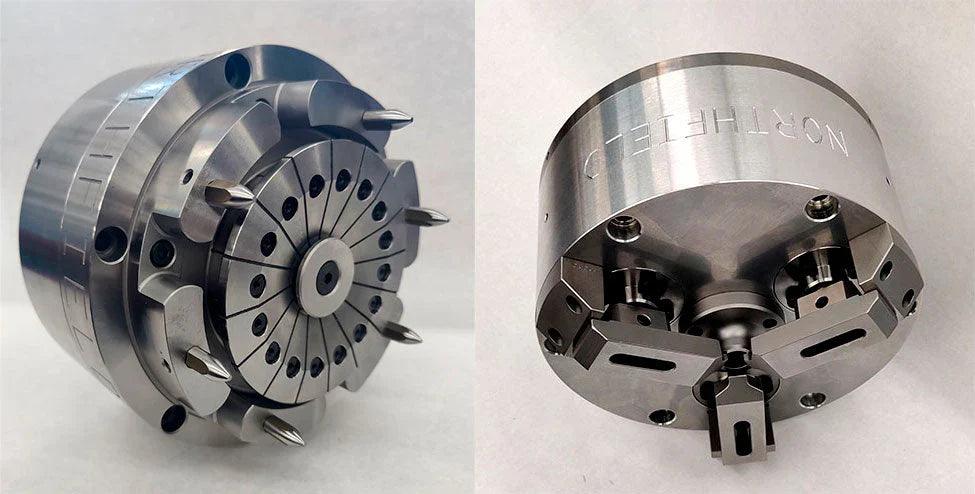
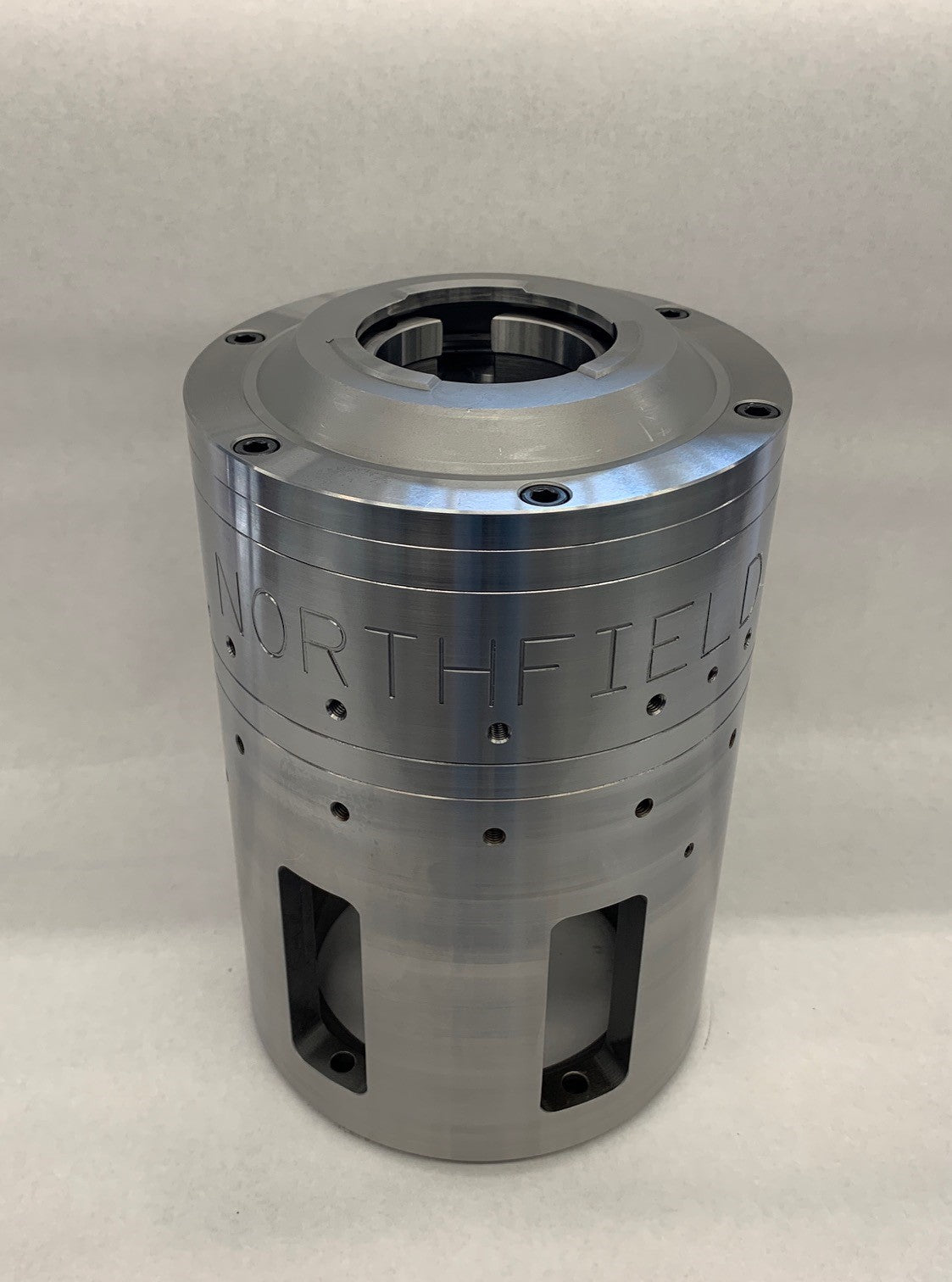
SPECIAL 7-IN. DIA. 10 IN. DEEP CHUCK
Special 7’’ Diameter Diaphragm Chuck with 2’’ counter bore center hole to swallow customer's work piece. Chuck has two independent diaphragm clamping plates to grip two separate diameters. Chuck is air open/spring clamp.With an overall height of 10’’, the customer has plenty of clearance for multiple oversized parts, without compromising work holding accuracy
Read More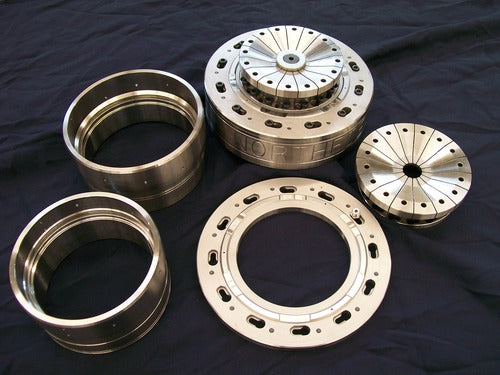
SPECIAL I.D. COLLET CHUCK
Special internal grip collet chuck / reverse diaphragm to grip transmission components for drilling. This chuck grips the I.D. and has “pull down”action. Special changeable stops have “air detect” part sensing to insure part is seated properly before cycle start. Chuck is air actuated with built in self contained air cylinder that can deliver up to 6,000 pounds of grip force. With (16) segments, this is true “full wrap” clamping.
Read More
7-IN, DIA. FACE CLAMPING FIXTURE WITH A MODEL 470 2-JAW MOUNTED IN THE CENTER
This is a face clamping chuck that has a standard Northfield model 470 mounted in the center to locate a transmission component on the root diameter while the fingers swivel intoposition and face clamp. The air chuck gently centers the part with no distortion while the fingers face clamp for grinding.
Read More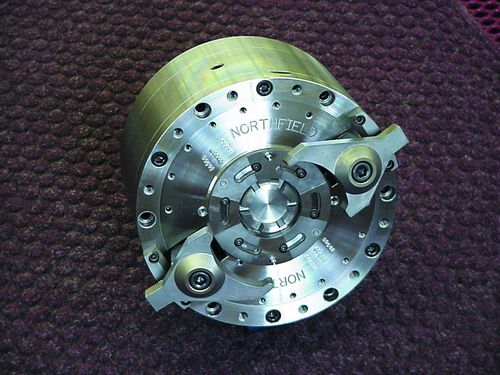
10-IN. DIA. FACE CLAMPING CHUCK
Special 10-inch diameter face-clamping chuck with adjustable orientating pins and center- mounted diaphragm plate to center workpiece before two contoured fingers swing into position to face-clamp aluminum pump housings for distortion-free boring at 4,000 rpm.
Read More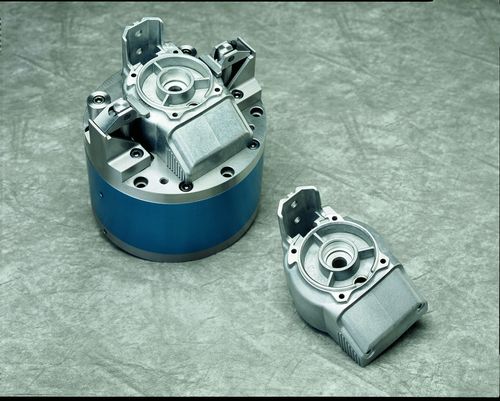
6-INCH DIA. PULL DOWN FIXTURE
This is a pull own clamp fixture. The part is a Bosch jig saw housing. Two pins mounted to chuck face locate the part and two face clamps rotate 90 degrees into position and comedown to clamp the part. Fixture rotates at 3,500 RPM to bore a bearing nest.
Read More
SPECIAL INTERNAL GRIP COLLET CHUCK
Specialized internal grip collet chuck with pull-down action and air detect part seat sensing. The pull-down action and air detect sensing ensure that the part is seated properly beforethe machine cycle starts. Chuck is used on a vertical machining center for rough and finish milling.
Read More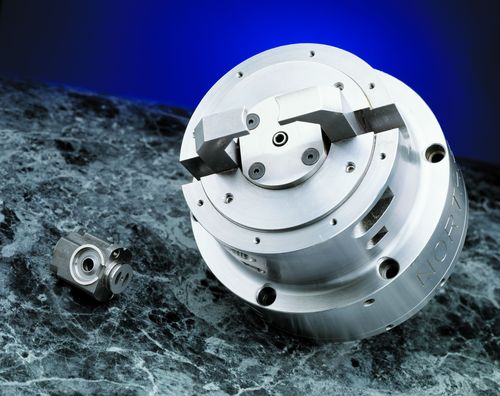
SPECIAL MULTI-ACTION 5 1/2-IN. DIA. PULL DOWN FIXTURE
SPECIAL MULTI-ACTION 5 1/2-IN. DIA. PULL DOWN FIXTURE
Read More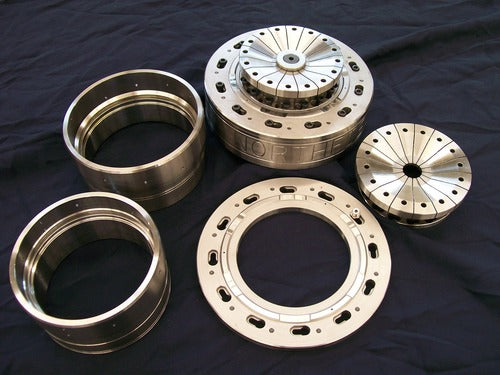
SPECIAL COLLET CHUCK
This is a 3 in. diameter hydraulically actuated internal grip collet chuck that mounts on a tilting table to drill an angled hole. A fixed stop pad picks up the inner face of thisautomotive work piece while the chuck expands and pulls back to grip the part. Chuck repeats to 1/10,000 T.I.R. and have a low profile to fit (8) chucks on one table.
Read More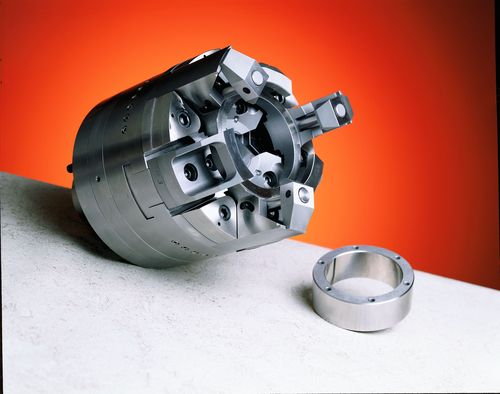
MODEL 700
Chuck is modified with 3 pull down fingers. Jaws have counter balance sub plates so jaws maintain 100% jaw force up to 6,000 RPM. Chuck is air open & spring clamp. Pull down fingersare independent. Chuck grips C.V. joint drive shafts, centers C.V. with jaws & pulls it down with fingers onto fixed stop. Shaft is balanced at 5-6,000 RPM. • T.I.R. – 1/10,000 • Axial – 1/10,000 • Cycle time 60 seconds
Read More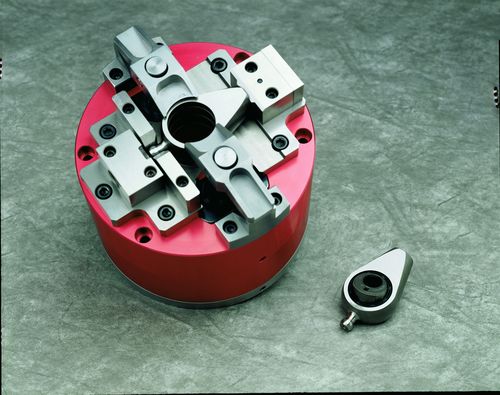
MODEL BIG RED
No, we’re not making a fashion statement for chucks here! At Northfield, we affectionately refer to the aluminum anodized chuck as “BIG RED” (it’s anodized red). “BIG RED” is usedby sub contractor Creed Monarch to manufacture close tolerance parts for Robert Bosch Power Tools. We designed “BIG RED” to accommodate the unusual shape of the “Wobble Plate” part of the drive mechanism of a Bosch reciprocating saw. The “Wobble Plate” is made from 52100 tool steel, heat-treated to 58/63 Rc. It is then spun to 3,500 rpm for hard turning the “Wobble Plate” I.D. which is in reality the outer race of a bearing set. “BIG RED” is yet another example of custom application “beyond the chuck.” Its spring-loaded plunger and locator ensure accurate locating of the “Wobble Plate” to four specific reference points or surfaces (see photo). When hand mounted on the face of a fixture, the unique design and accuracy of the fixture provide repeatability of 0.002 inches. “BIG RED” solved the previous holding problems and in addition, saved a tremendous amount of production time, since the fixture allows automatic operation after the initial hand loading
Read More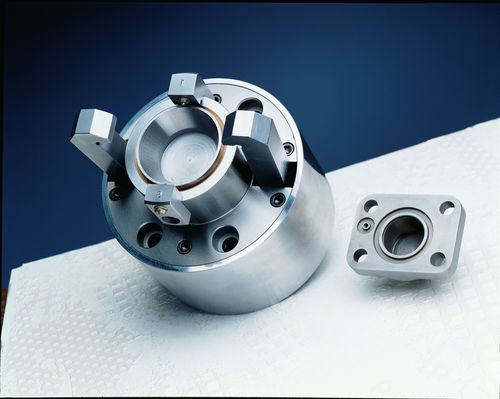
PULL DOWN CHUCK
Special Drawbar-Actuated, Pull Down Chuck with Centered Pilot Here is a great example of how Northfield’s creative engineering helps customers solve tough workholdingproblems. When a special chuck was needed to hold an unusually shaped automotive part, Northfield was asked for ideas. The machining operation was basic, hard turn a straight bore that is case hardened to 58/63 Rockwell “C”. The complicating factor was the shape of the part; it was not round or concentric. The straight bore must be machined concentric to a cone shaped hub and perpendicular to a larger offset rectangular flange. After reviewing the problem, Paul DeFeo, Chief Engineer at Northfield, realized that the most accurate way to hold the part was to grip it by the cone and bank off the flange. The question was how, since the cone surface was too steep to be gripped by conventional chuck jaws. The solution was to design a special drawbar-actuated, pull-down chuck with a spring- loaded funnel shaped base that was a female version of the cone shape on the part. This base fits into the chuck body with a zero clearance sliding fit. The operator pushes the part down into the funnel, two spring loaded ball plungers hold the part in place, allowing the operator to move his hands away from the work area before activating the chuck. Upon actuation, clamping arms swing over and down onto the part’s flange. The spring loaded funnel base picks up the cone for centralization and slides into the chuck as the flange comes to a fixed stop for axial location and clamping. After machining, the arms retract and the part is pushed up and out for easy removal. How is this “not just chucks” approach working? Using our chuck, this application runs 24 hours a day, seven days a week, producing parts with outstanding accuracy and repeatability.
Read More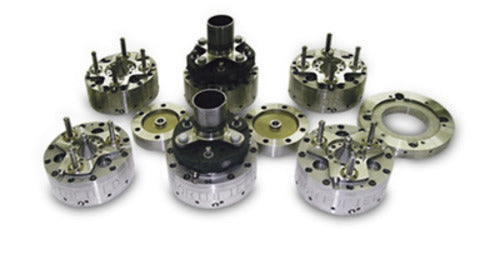
SPECIAL DRIVESHAFT BALANCE FIXTURES
These custom chucks use a special expanding collet to center the drive-shaft end, and (3) or (4) fingers go through the bolt holes, expand and face clamp.
Read More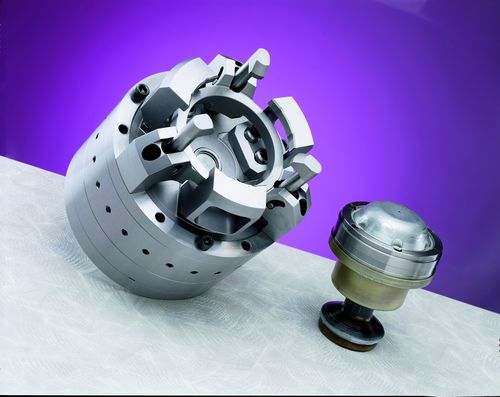
7-IN. DIAPHRAGM CHUCK
Special 7-inch diameter counter-balanced diaphragm chuck with 3 pull down fingers. Jaws grip O.D. of C.V. joint while fingers pull it into the fixed axial stop for zero axial location. Chuckrotates 5 – 6,000 rpm to balance C.V. joint drive shafts. • T.I.R. = 50 millionths • Axial = 0 • Cycle time 60 sec.
Read More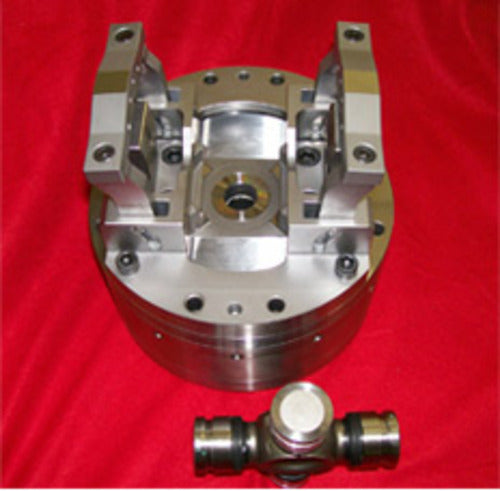
HIGH SPEED BALANCING CHUCK
This fixture locates a universal joint using built-in V-Blocks and (2) diaphragm jaws. The jaws and blocks center the workpiece while 2 arms slide down to face clamp.
Read More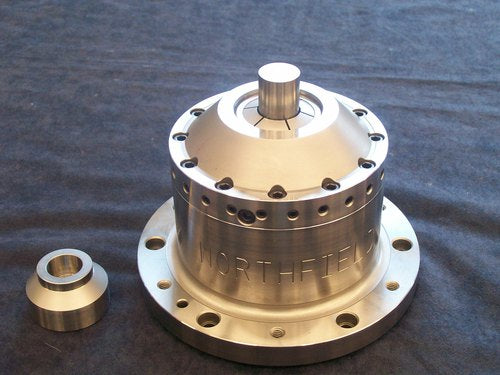
SPECIAL GIMBALING COLLET CHUCK
This chuck uses a special precision collet to grip the pitch diameter of a splined drive shaft for balancing. The collet taper is ground inside a sphere which is then installed tothe mating sphere, allowing the collet to “gimbal”. When a drive shaft is placed in a balance machine, it “whips” due to the unbalance. If the chuck holds the shaft rigid (not allowing whip,the shaft is falsely balanced with poor results. This chuck cuts the balance cycle in half with superior accuracy. Chuck is push to open and spring clamp.
Read More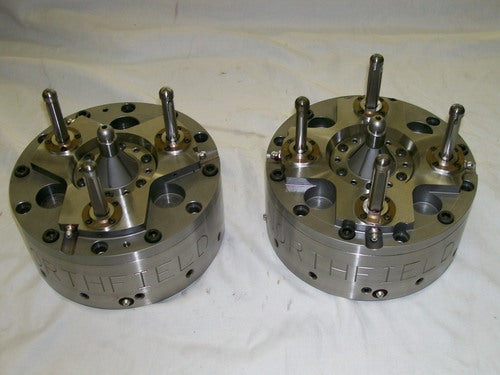
7" DIAMETER COLLET CHUCK
These custom 7" diameter chucks use the small internal-grip collet to center the workpiece while the outer “spit fingers” face the clamp. The collet is spring-clamp/draw-bar open. The splitfingers are actuated by the draw bar. The fingers go inside the bolt-hole, expand and face clamp, mimicking how a bolt would hold the part. The chucks are used for balancing drive shafts and grip what is called a “rubber coupling” at speeds up to 6,000 rpm.
Read More